Rope Access Equipment - Selection & Inspection
This is a subtitle for your new post
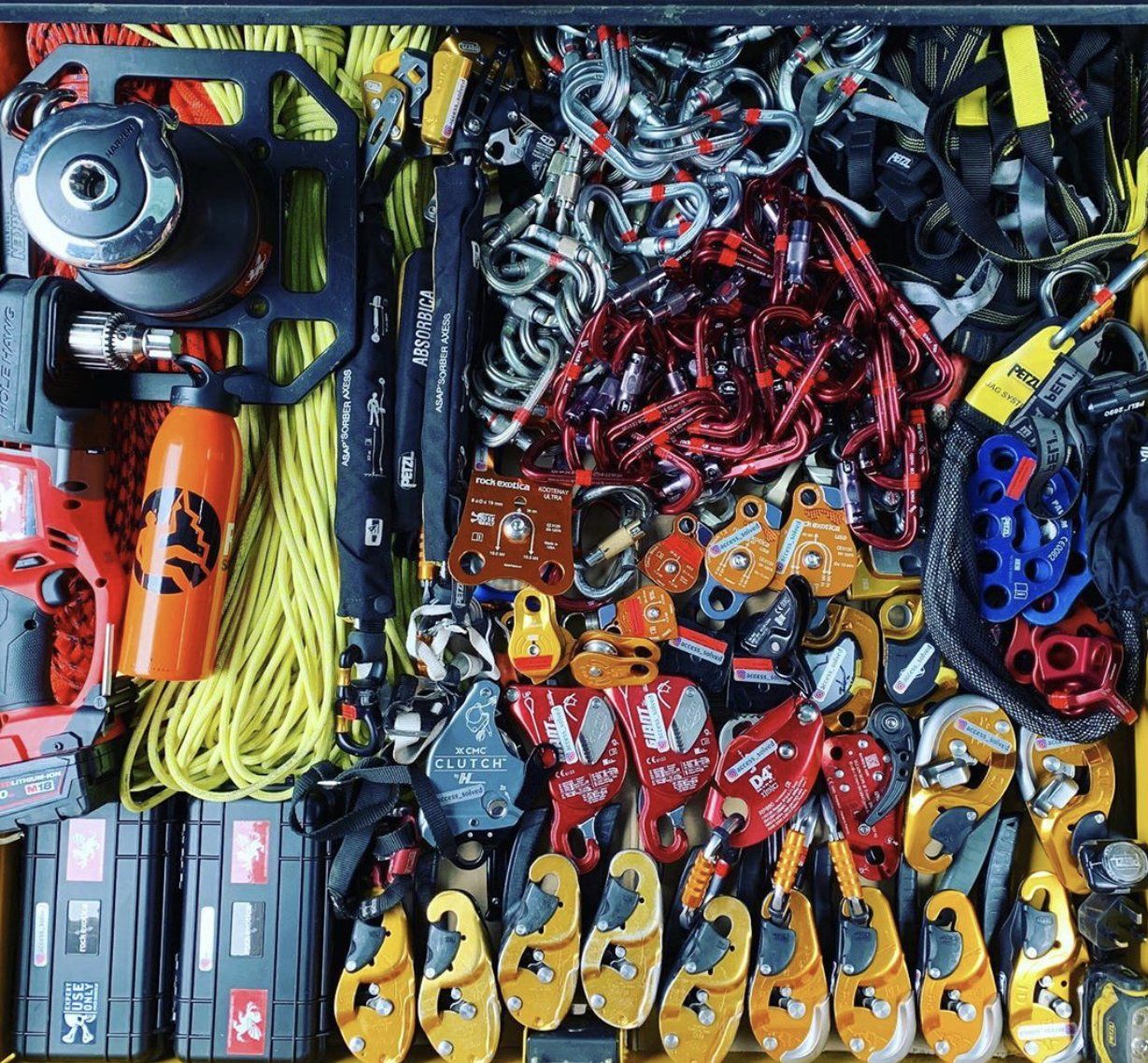
An assessment should be carried out before each job to select the most appropriate equipment to be used. (IRATA ICoP 2.7.1.1)
How many times have we just ordered a piece of kit, that we have never used or had any experience with? Do we read the instructions? Do we get it inspected? Hopefully this will cast some light on the do's and don'ts.
So as a start we have to know the laws and regulations, Again as with the other articles I didn't want it to be a bombardment of quotes from regulation documents. But we have to know the facts. I have condensed a lot of it down and put where to find the information if you want to delve more into it.
So no doubt you have heard of LOLER
What is LOLER?
Lifting Operations and Lifting Equipment Regulations 1998 place duties on people and companies who own, operate or have control over lifting equipment. This includes all businesses and organisations whose employees use lifting equipment, whether owned by them or not. In most cases, lifting equipment is also work equipment so the Provision and Use of Work Equipment Regulations (PUWER) will also apply (including inspection and maintenance). All lifting operations involving lifting equipment must be properly planned by a competent person, appropriately supervised and carried out in a safe manner.
LOLER also requires that all equipment used for lifting is fit for purpose, appropriate for the task, suitably marked and, in many cases, subject to statutory periodic 'thorough examination'. Records must be kept of all thorough examinations and any defects found must be reported to both the person responsible for the equipment and the relevant enforcing authority.
Lifting equipment includes any equipment used at work for lifting or lowering loads (including persons), including attachments used for anchoring, fixing or supporting it. So in our case, as Rope Access technicians, Ropes, Harnesses, Karabiners and connectors, Slings and Strops etc all fall under LOLER.
How do we select of equipment?
So how do you select the equipment you use? research? prior experience? recommendation? or are you just given a kit or equipment to use?
There should be an assessment before each job is carried out to find the most appropriate equipment to be used. The assessment should also pay special attention to the probability and consequences of misuse of equipment, taking into account any known incidents, e.g. as detailed in IRATA International safety bulletins. The selection and purchase of equipment should be carried out by, or approved by, a competent person, who has sufficient knowledge of the technical specifications required (IRATA 2.7.1.1)
The ICOP goes into the legal requirements and the standards that equipment should conform, I won't list all the EN numbers for all the kit but for anyone that is interested the information can be found on page 21 of the ICOP and Annex C.
If you are using a piece of Rope Access equipment for the first time you must:
- read and understand all the instructions for use.
- Get specific training in its proper use (You can record this within your log book)
- Become acquainted with its capabilities and limitations.
- Understand and accept the risks involved.
So if you come across a piece of equipment you are unfamiliar with, don't be afraid to say so, There is no shame in not knowing something, the shame comes from not asking. If you have a competent Level 3 or equivalent and they are familiar themselves with said piece of kit, get them to run through the safe operation of it. This should be noted in the Toolbox Talk that the device has been fully explained and this should be signed to say you are happy with the use and instruction.
Where to purchase?
So you may or may not be involved in the purchase of equipment. As previously stated the selection and purchase of equipment should be carried out by, or approved by, a competent person, who has sufficient knowledge of the technical specifications required.
Now as I have said in previous articles, I live in the real world, I know there are individuals out there that want to buy kit for the cheapest price possible or pick up second had stuff. Reality is you want to be using a reputable retailer/supplier of Rope Access equipment. Don't be tempted to buy off a bidding site or a social media market place. At the end of the day this is equipment that you are entrusting yours or someone else's life to.
I personally use Abaris, the link is above. Will and the guys have always got what we need and if they don't they are quick to source. I do use other suppliers but I'd say 85% of equipment I get from Abaris.
So with the equipment comes the manufacturers instructions, sales invoice and certificate of conformity (Keep these!). Ideally you want to purchase equipment that has a unique serial number. This will aid in cross referencing with respective documentation (Traceability).
There is more information to be found on this in the IRATA ICOP 2.8.1 and ISO-22846 6.5.1
As I have said above getting kit with unique serial numbers makes life a bit easier. (For example some karabiners come with a batch number rather than a individual serial number) If for whatever your reason go for karabiners with batch numbers, I would recommend tough tags. These are tags that you can have printed with your own serial numbers and other information. I have been impressed at their longevity on kit that has been worked hard.
Periodic Thorough Examinations
We all get told this on our IRATA and BS7985/ISO22846 courses, LOLER actually word it slightly differently to that of IRATA. But the three kinds of inspection or examination we will hopefully know about are:
- Pre Use Check - consists of a visual and tactile inspection, which should be carried out before first use each day
- Detailed Inspection or "6 monthly" - This is the formal thorough inspection of the equipment carried out by a competent person. (We'll go into competency shortly)
- Interim Inspection - So I always remember IRATA's wording for this one, its an inspection of your kit after arduous or exceptional events, example of this would be you have been using a chemical, brick cleaner or used it in a incinerator when it was very dusty or gritty.
So do you undertake a pre use check? Do you get your kit checked by a competent person every 6 months? Do you have a interim inspection done after arduous or exceptional use?
So who's competent to inspect your kit?
For Pre use checks, As qualified Rope access technicians we should all be comfortable in what we are looking at and what to look out for. There is no need to record pre use checks (unless a defect is found or it is your employing companies policy to do so).
For the undertaking of a detailed (6 monthly) or interim inspection you have to be a competent person.
The term 'competent person' is not defined in law but the LOLER Approved Code of Practice and guidance(paragraph 294 on competent persons) states that:
'You should ensure that the person carrying out a thorough examination has such appropriate practical and theoretical knowledge and experience of the lifting equipment to be thoroughly examined as will enable them to detect defects or weaknesses and to assess their importance in relation to the safety and continued use of the lifting equipment.'
So can you inspect your own equipment?
IRATA says "2.10.1.5 It is essential that the person carrying out a detailed or interim inspection has the authority to discard equipment and is sufficiently competent, independent and impartial to allow objective decisions to be made."
But they also say that " A competent person may exist within a rope access company."
LOLER 1998 says " The person must be independent from the employer’s line management. The competent person can be in-house or from an external organisation such as an insurance company."
I think the important thing is to be professional, Do you really want to pass a piece of equipment that could jeopardise yours or others safety? Thats not just you inspecting your own kit, Do you inspect others kit? As LOLER says you should have appropriate practical and theoretical knowledge and experience of the equipment to be examined.
How should equipment information be recorded?
If you are the competent person in charge of equipment and inspection then you will probably be aware of the different ways you can record all the information of the equipment. These vary from a simple excel spreadsheet to PPE management software.
So the simplest way is an excel spread sheet, It can be a bit of a laborious task to start with but once you have created your database it is easy to update accordingly.
If you are looking at PPE management software, then you may want to look at Papertrail. They have developed a cloud based system which allows hassle free record keeping and has a good notification system where it will alert you when a piece of equipment is due for inspection. More details can be found on their website.
So I hope this has been a useful read, I hope if you can take anything from this it will be to become more professional and safer in your approach towards working.
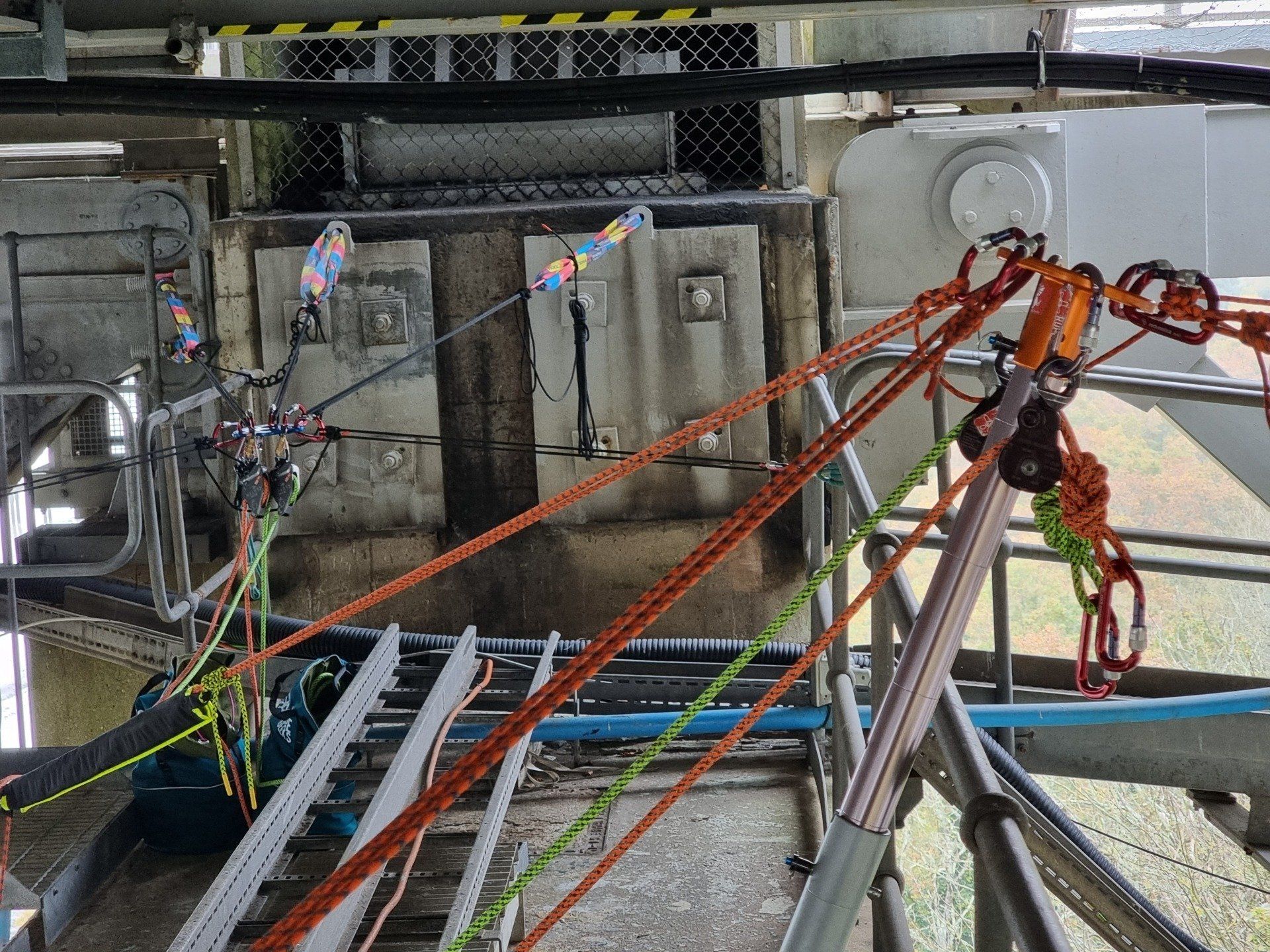
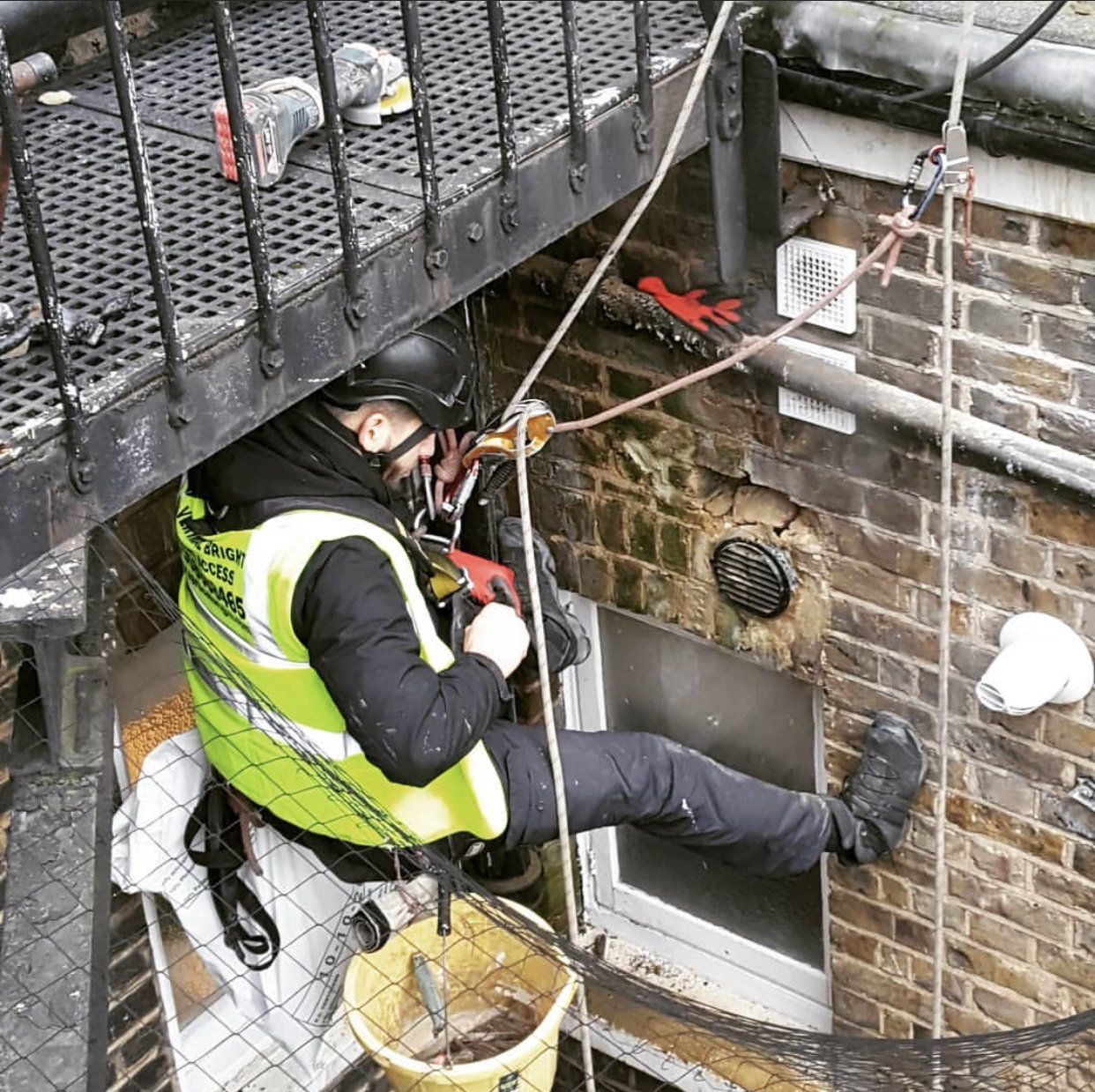
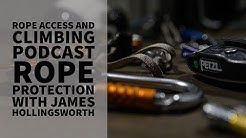
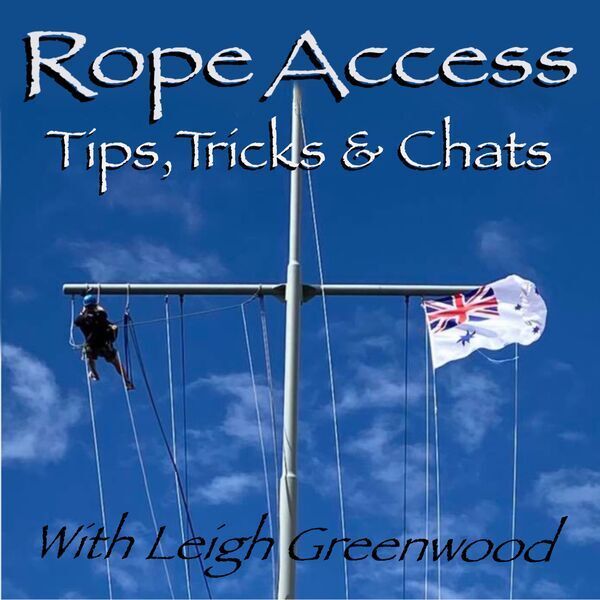